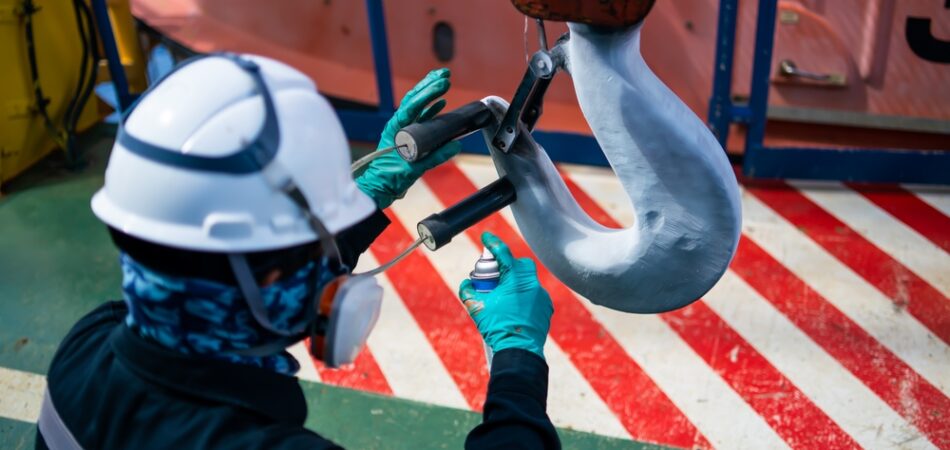
Cranes are an essential component of many industries, from construction and manufacturing to shipping and logistics. They are responsible for lifting and transporting heavy loads, making them crucial to the efficiency and safety of various operations. However, due to the constant stress and strain they endure, cranes are susceptible to wear and tear, which can lead to structural failures if not properly inspected and maintained. This is where non-destructive testing crane inspections come into play.
Non-destructive testing (NDT) is a collection of techniques used to assess the integrity of materials and components without causing damage. It allows inspectors to identify hidden defects, cracks, or other issues that could compromise the safety and reliability of crane operations. By implementing NDT safety inspections Arizona businesses can ensure that their cranes remain in optimal working condition, reducing the risk of accidents, equipment failure, and costly downtime. The ability to detect potential issues before they become critical helps businesses maintain a safe working environment and comply with industry regulations.
Common Non-Destructive Testing Methods for Crane Safety Inspections
A variety of NDT techniques are utilized to assess the structural and mechanical integrity of cranes. Each method has its own advantages and is chosen based on the specific requirements of the inspection. One of the most widely used techniques is visual inspection, which involves a thorough examination of crane components to detect visible signs of wear, corrosion, or deformation. While visual inspections are crucial, they are often complemented by more advanced NDT methods to identify hidden defects.
Ultrasonic testing (UT) is another popular method used in non-destructive testing crane inspections. This technique employs high-frequency sound waves to detect cracks, voids, or inconsistencies within metal structures. By analyzing the reflections of these sound waves, inspectors can determine the location and severity of internal defects without damaging the material.
Magnetic particle testing (MPT) is commonly used to inspect ferromagnetic materials for surface and near-surface cracks. By applying a magnetic field and ferrous particles to the crane components, inspectors can easily identify flaws that could compromise structural integrity. Similarly, dye penetrant testing (DPT) is employed to detect surface defects in non-porous materials. This method involves applying a special liquid dye to the surface, which penetrates cracks and reveals defects under ultraviolet or visible light.
Radiographic testing (RT), which utilizes X-rays or gamma rays, is highly effective in detecting internal flaws that are not visible through other inspection methods. This technique produces detailed images of the internal structure of crane components, allowing inspectors to identify defects such as voids, cracks, or welding inconsistencies. By employing these NDT methods, reliable crane testing Chandler businesses can ensure their equipment is free from defects that could lead to operational failures.
The Role of NDT in Preventing Crane Failures and Accidents
Cranes operate under immense mechanical and environmental stress, which can lead to material fatigue, corrosion, and structural weaknesses over time. If these issues are not addressed promptly, they can result in catastrophic failures, posing serious risks to workers and equipment. Regular non-destructive testing crane inspections play a crucial role in preventing such incidents by providing early detection of potential problems.
One of the primary causes of crane failures is metal fatigue, which occurs when repeated loading and unloading weaken the material over time. NDT methods such as ultrasonic testing and radiographic testing can identify early signs of fatigue before they progress into critical failures. Similarly, corrosion can weaken metal structures and lead to unexpected breakdowns. Magnetic particle testing and dye penetrant testing help detect corrosion-related defects, ensuring that necessary repairs or replacements are carried out in a timely manner.
Structural welds are another critical aspect of crane safety. Poor welding quality or defects such as cracks, lack of fusion, or porosity can compromise the overall strength of a crane. NDT safety inspections Arizona businesses rely on advanced inspection techniques to evaluate weld integrity, ensuring that crane components remain strong and durable. By identifying weak points and defects before they cause major issues, NDT helps companies prevent accidents, enhance operational efficiency, and extend the lifespan of their equipment.
Regulatory Compliance and Industry Standards for Crane Inspections
Crane inspections are not just a matter of operational efficiency; they are also a legal requirement in many industries. Regulatory bodies such as the Occupational Safety and Health Administration (OSHA) and the American Society of Mechanical Engineers (ASME) establish strict guidelines for crane inspections and maintenance. Compliance with these standards is essential to avoid penalties, ensure worker safety, and maintain business credibility.
Non-destructive testing crane inspections play a significant role in helping businesses meet these regulatory requirements. Regular NDT inspections ensure that cranes are operating within safety standards and help companies maintain detailed records of their maintenance history. These records are essential for demonstrating compliance during audits and inspections.
In addition to federal and state regulations, many industries have their own specific safety standards that require reliable crane testing Chandler companies to implement routine NDT inspections. For instance, the construction and maritime industries have stringent safety protocols that mandate frequent crane inspections to prevent workplace accidents. By integrating NDT into their maintenance programs, businesses can ensure compliance with industry regulations while maintaining the highest levels of safety and reliability.
The Future of NDT in Crane Inspections and Advancements in Technology
As technology continues to evolve, so do the methods used for non-destructive testing crane inspections. Advancements in NDT techniques are making inspections more efficient, accurate, and cost-effective, further enhancing crane safety and reliability. One of the most promising developments in this field is the use of automated and robotic inspection systems. These systems can access hard-to-reach areas, perform detailed inspections with minimal human intervention, and provide real-time data analysis to detect defects more efficiently.
Another major advancement is the integration of artificial intelligence (AI) and machine learning in NDT safety inspections Arizona businesses. AI-powered analysis can process large amounts of inspection data, identify patterns, and predict potential failures before they occur. This predictive maintenance approach allows companies to address issues proactively, reducing unexpected downtime and repair costs.
Additionally, digital imaging and 3D scanning technologies are revolutionizing reliable crane testing Chandler companies by providing highly detailed visualizations of crane components. These technologies enable inspectors to detect even the smallest defects with greater precision, improving the overall effectiveness of NDT inspections. The use of drone technology is also gaining traction, allowing inspectors to conduct aerial assessments of large cranes and structures without the need for extensive scaffolding or manual climbing.
Conclusion
The continuous improvement of NDT techniques ensures that crane inspections remain at the forefront of safety and reliability. By adopting the latest innovations in non-destructive testing, businesses can enhance their maintenance strategies, reduce risks, and ensure the long-term performance of their crane operations. As safety standards evolve and technology advances, NDT will continue to play a crucial role in the safe and reliable operation of cranes across various industries.
Need a Crane Inspector in Chandler, AZ?
American Inspection and Test, Inc. is a family owned and operated crane and aerial lift inspection service with 20 years of experience. Our mission is to elevate safety through a higher quality of certified inspectors and have a better standard testing and inspection procedures overall. We are known for our high standards and work ethic and have been recognized by multiple national, federal, state and city agencies. Increase safety and lower maintenance costs by calling us today.